In recent years, the term "Russian lathe incident" has sparked widespread curiosity and concern across the globe. This chilling event, shrouded in mystery, has become a topic of intense discussion, raising questions about safety standards, industrial practices, and human error. Whether you're hearing about it for the first time or seeking a deeper understanding, this article aims to shed light on the incident while exploring its broader implications. With a focus on clarity, accuracy, and engagement, we will unravel the layers of this story to provide a comprehensive perspective.
At its core, the "Russian lathe incident" refers to a harrowing industrial accident that occurred in a Russian manufacturing facility. While the exact details remain somewhat murky due to limited official reports, the event has been widely documented through online forums, videos, and anecdotal accounts. The incident not only highlights the dangers inherent in industrial machinery but also serves as a sobering reminder of the importance of workplace safety protocols. It has captured the attention of engineers, safety experts, and curious onlookers alike, prompting discussions about how such tragedies can be prevented in the future.
As we delve deeper into the topic, we will explore not only the incident itself but also its ripple effects on industries worldwide. From examining the causes and consequences to analyzing the lessons learned, this article will provide a holistic view of the "Russian lathe incident." By the end, readers will gain valuable insights into the importance of vigilance, accountability, and innovation in ensuring safer working environments. So, buckle up as we embark on a journey to uncover the truth behind this infamous event.
Read also:Unveiling Mysteries Of El Chapos Hidden Fortune Estimating His Net Worth
Table of Contents
- What Really Happened in the Russian Lathe Incident?
- Why Did the Russian Lathe Incident Occur?
- How Can Industries Learn from the Russian Lathe Incident?
- The Role of Human Error in Industrial Accidents
- What Are the Long-Term Effects of the Russian Lathe Incident?
- How Does the Russian Lathe Incident Compare to Other Industrial Disasters?
- What Safety Measures Can Prevent Future Incidents?
- Frequently Asked Questions About the Russian Lathe Incident
What Really Happened in the Russian Lathe Incident?
The "Russian lathe incident" is a term that has become synonymous with industrial accidents, and for good reason. The event unfolded in a Russian manufacturing plant, where a lathe—a machine used for shaping metal or wood—was being operated under questionable conditions. While official reports are scarce, multiple sources suggest that the incident involved a catastrophic failure of the machine, leading to severe consequences for those involved. The exact timeline of events is debated, but the core narrative remains consistent: a combination of mechanical failure, improper use, and inadequate safety measures culminated in a horrifying accident.
Witness accounts and online videos depict a scene of chaos and devastation. It is believed that the operator of the lathe either ignored or was unaware of critical safety protocols, leading to a chain reaction that resulted in the machine malfunctioning. The incident not only caused physical harm but also left a lasting psychological impact on those who witnessed it. Some reports suggest that the operator was ejected from the machine, while others describe a gruesome entanglement with the equipment. Regardless of the specifics, the event serves as a stark reminder of the dangers posed by industrial machinery when proper precautions are not taken.
One of the most unsettling aspects of the "Russian lathe incident" is the lack of transparency surrounding it. While some details have emerged through unofficial channels, there is no comprehensive investigation or report to provide a definitive account. This absence of clarity has fueled speculation and misinformation, making it difficult to separate fact from fiction. However, one thing is certain: the incident has become a cautionary tale, prompting industries worldwide to reevaluate their safety standards and practices. By examining the circumstances that led to this tragedy, we can better understand how to prevent similar occurrences in the future.
Why Did the Russian Lathe Incident Occur?
To fully comprehend the "Russian lathe incident," it is essential to explore the underlying causes that contributed to the tragedy. Industrial accidents rarely result from a single factor; instead, they are often the culmination of multiple issues, ranging from mechanical failures to human error. In this case, several key factors appear to have played a role, each exacerbating the risks associated with operating heavy machinery.
Was the Equipment Properly Maintained?
One of the most pressing questions surrounding the "Russian lathe incident" is whether the equipment involved was properly maintained. Lathes, like all industrial machinery, require regular inspections and servicing to ensure they function safely and efficiently. Neglecting these maintenance routines can lead to mechanical failures, which may have catastrophic consequences. In this instance, it is believed that the lathe in question had not undergone the necessary checks, resulting in a critical malfunction during operation. This raises concerns about the overall maintenance culture within the facility and highlights the importance of adhering to strict maintenance schedules.
Were Safety Protocols Followed?
Another critical factor to consider is whether safety protocols were followed during the operation of the lathe. Safety measures, such as wearing protective gear, using machine guards, and adhering to operational guidelines, are designed to minimize the risk of accidents. However, reports suggest that these protocols were either ignored or inadequately enforced in this case. For instance, it is alleged that the operator was not wearing the required protective equipment, which may have contributed to the severity of the incident. Additionally, the absence of machine guards—a common safety feature—likely increased the likelihood of entanglement or ejection. These lapses underscore the need for rigorous training and enforcement of safety standards in industrial settings.
Read also:Don Henley Net Worth A Detailed Financial Overview
What Role Did Human Error Play?
Human error is often a significant contributor to industrial accidents, and the "Russian lathe incident" is no exception. Whether due to inexperience, fatigue, or complacency, the operator's actions—or lack thereof—may have played a pivotal role in the tragedy. For example, operating the machine at an unsafe speed or attempting to make adjustments while it was still running could have triggered the catastrophic failure. Furthermore, the absence of proper supervision may have allowed these risky behaviors to go unchecked. This highlights the importance of fostering a culture of accountability and continuous learning within industrial environments.
Ultimately, the "Russian lathe incident" serves as a sobering reminder of the complex interplay of factors that can lead to industrial accidents. By addressing issues such as equipment maintenance, safety protocols, and human error, industries can take meaningful steps toward preventing similar tragedies in the future.
How Can Industries Learn from the Russian Lathe Incident?
The "Russian lathe incident" offers a wealth of lessons for industries worldwide, serving as a stark reminder of the importance of safety, accountability, and continuous improvement. By analyzing the factors that contributed to this tragedy, organizations can implement strategies to mitigate risks and create safer working environments. Here, we explore some of the key takeaways and actionable steps that industries can adopt to prevent similar incidents in the future.
What Safety Measures Can Be Enhanced?
One of the most immediate lessons from the "Russian lathe incident" is the critical need for enhanced safety measures. Industries must prioritize the implementation of comprehensive safety protocols that address every aspect of machine operation. This includes:
- Regular Maintenance: Establishing a rigorous maintenance schedule to ensure all machinery is in optimal condition.
- Protective Equipment: Mandating the use of personal protective equipment (PPE) for all operators and ensuring it is readily available.
- Machine Guards: Installing and maintaining machine guards to prevent entanglement or ejection during operation.
How Can Training Programs Be Improved?
Another crucial area for improvement is operator training. Many industrial accidents, including the "Russian lathe incident," can be attributed to insufficient training or a lack of awareness about potential risks. To address this, industries should:
- Comprehensive Training: Develop training programs that cover not only machine operation but also emergency procedures and risk management.
- Continuous Education: Encourage ongoing education and refresher courses to keep operators updated on best practices.
- Simulated Scenarios: Use simulations and drills to prepare operators for real-life emergencies.
What Role Does Leadership Play in Safety Culture?
Leadership plays a pivotal role in fostering a culture of safety within an organization. By prioritizing safety and leading by example, management can instill a sense of responsibility and accountability among employees. Key strategies include:
- Open Communication: Encouraging open dialogue about safety concerns and fostering an environment where employees feel comfortable reporting hazards.
- Accountability: Holding all levels of the organization accountable for adhering to safety protocols.
- Recognition: Rewarding individuals and teams who demonstrate a commitment to safety.
By implementing these measures, industries can transform the lessons of the "Russian lathe incident" into actionable steps that enhance safety and prevent future tragedies.
The Role of Human Error in Industrial Accidents
Human error is a pervasive and often underestimated factor in industrial accidents, including the infamous "Russian lathe incident." While machinery and external conditions play a significant role, it is the human element that often tips the scales toward disaster. Understanding the nuances of human error in such contexts is crucial for preventing future accidents and fostering a safer industrial environment.
What Are the Common Types of Human Error in Industrial Settings?
Human error in industrial accidents can manifest in various forms, each with its own set of risks and consequences. Some of the most common types include:
- Misjudgment: Operators may misjudge the speed, pressure, or timing required for a task, leading to unintended outcomes.
- Complacency: Overconfidence or routine-induced complacency can result in the neglect of safety protocols.
- Fatigue: Physical or mental exhaustion can impair decision-making and reaction times, increasing the likelihood of mistakes.
- Lack of Training: Insufficient knowledge or experience can lead to improper handling of machinery or failure to recognize hazards.
How Can Human Error Be Minimized in Industrial Environments?
While human error cannot be entirely eliminated, it can be significantly reduced through targeted interventions and systemic improvements. Here are some strategies to consider:
- Standard Operating Procedures (SOPs): Clearly defined SOPs can guide operators through tasks, reducing the margin for error.
- Ergonomic Design: Designing workspaces and machinery to minimize physical strain can help reduce fatigue-related errors.
- Automated Systems: Implementing automation for repetitive or high-risk tasks can reduce reliance on human intervention.
- Regular Breaks: Encouraging regular breaks and rotation of tasks can help mitigate the effects of fatigue.
What Are the Psychological Factors Behind Human Error?
Psychological factors often underpin human error, and understanding these can provide deeper insights into accident prevention. Stress, anxiety, and cognitive overload can impair an operator's ability to focus and make sound decisions. Additionally, the pressure to meet production targets may lead to shortcuts or risky behaviors. Addressing these psychological factors through supportive work environments, stress management programs, and realistic performance expectations can go a long way in reducing human error.
By acknowledging the role of human error and implementing measures to mitigate it, industries can create a more resilient and accident-resistant workplace. The lessons from the "Russian lathe incident" underscore the importance of addressing not just the mechanical aspects of safety but also the human elements that contribute to industrial accidents.
What Are the Long-Term Effects of the Russian Lathe Incident?
The "Russian lathe incident" has left a lasting impact that extends far beyond the immediate aftermath of the tragedy. Its long-term effects resonate across industries, influencing safety standards, public perception, and even legislative frameworks. By examining these enduring consequences, we can better appreciate the incident's broader significance and the steps being taken to prevent similar occurrences in the future
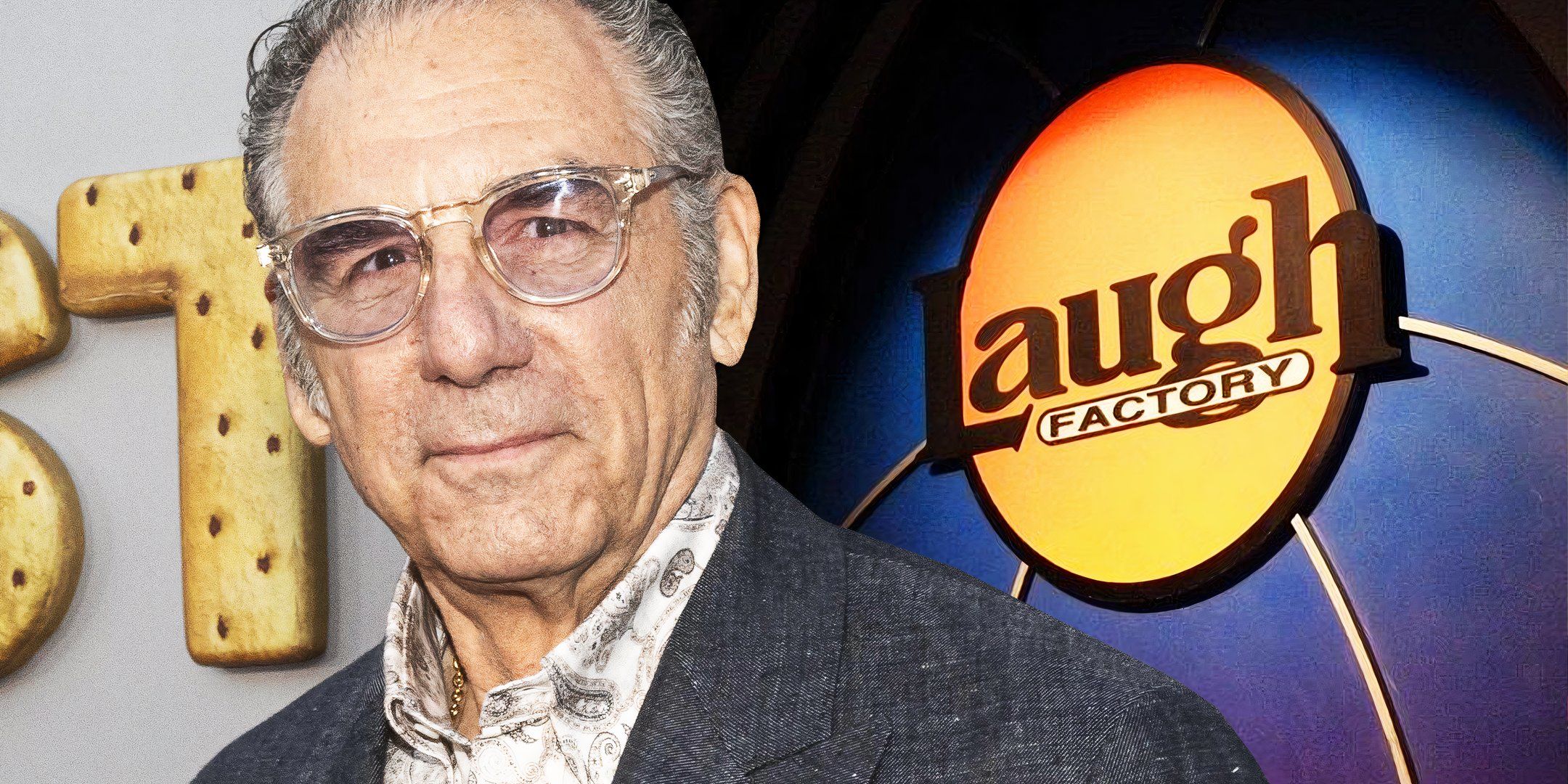
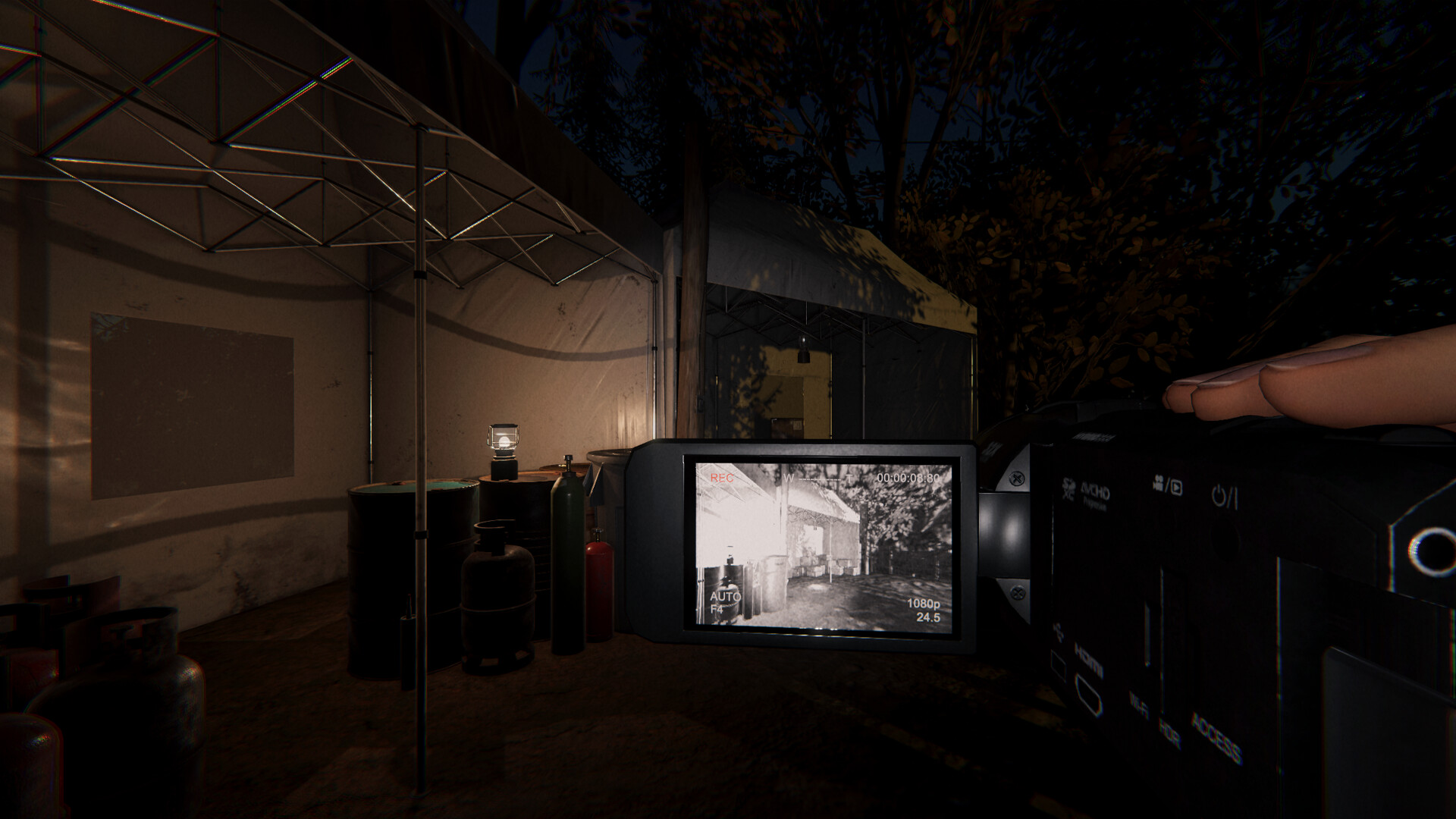