From construction sites to art restoration studios, these tools have revolutionized the way tasks are performed. Whether you’re a professional contractor or a DIY enthusiast, understanding the capabilities of blasters can open up a world of possibilities. In this guide, we’ll explore their applications, benefits, and much more to help you harness their full potential. Blasters come in various forms, each tailored to specific tasks. For instance, sandblasters are commonly used for surface preparation, while air blasters are ideal for material handling in industrial settings. Their ability to deliver high-pressure streams of media makes them invaluable for tasks requiring precision and power. As we dive deeper into the topic, we’ll uncover how blasters have evolved over time and why they remain a cornerstone of modern-day operations. The growing demand for efficiency and precision in industrial and creative fields has fueled the popularity of blasters. Their adaptability ensures they remain relevant in an ever-changing technological landscape. By the end of this article, you’ll have a comprehensive understanding of blasters, their uses, and how they can elevate your projects. So, let’s embark on this journey to explore the world of blasters and discover why they’re a game-changer.
Table of Contents
- What Are Blasters and How Do They Work?
- Different Types of Blasters and Their Unique Features
- Why Are Blasters Essential in Modern Industries?
- How to Choose the Right Blasters for Your Needs
- What Are the Safety Tips for Using Blasters?
- Frequently Asked Questions About Blasters
- The Future of Blasters: Innovation and Advancements
- Conclusion: Unlocking the Full Potential of Blasters
What Are Blasters and How Do They Work?
Blasters are powerful tools designed to propel abrasive materials or air at high speeds to achieve specific tasks. These tools operate on the principle of pressurized force, where air, water, or another medium is used to propel particles or create movement. The core mechanism involves a compressor or generator that builds up pressure, which is then released through a nozzle to direct the stream. This process is what makes blasters so effective in tasks requiring precision and power.
There are several components that make up a typical blaster system. These include the compressor, nozzle, hose, and media container. The compressor generates the necessary pressure, while the nozzle controls the direction and intensity of the stream. The hose serves as the conduit for the medium, ensuring it reaches the target area efficiently. Depending on the type of blaster, the media used can vary from sand and water to steel grit or even dry ice. Each medium is chosen based on the task at hand, whether it’s cleaning, cutting, or surface preparation.
Read also:Secrets Of Success Bargain Block Guys Net Worth
Understanding how blasters work is crucial for maximizing their potential. For example, in industrial settings, blasters are often used to remove rust or paint from metal surfaces. The abrasive particles are propelled at high speeds, effectively stripping away unwanted layers without damaging the underlying material. Similarly, in creative fields, blasters are used for etching designs into glass or stone, showcasing their versatility. By mastering the mechanics of blasters, users can achieve remarkable results while maintaining efficiency and precision.
Different Types of Blasters and Their Unique Features
Blasters come in various forms, each designed to cater to specific applications. Understanding the differences between these types can help you choose the right tool for your needs. Below, we’ll explore some of the most common types of blasters and their unique features.
Sandblasters: The Workhorse of Surface Preparation
Sandblasters are perhaps the most well-known type of blasters. They use sand or other abrasive materials to clean, strip, or etch surfaces. Sandblasters are widely used in industries such as automotive, construction, and marine maintenance. Their ability to remove rust, paint, and grime quickly makes them indispensable for surface preparation tasks.
Water Blasters: Eco-Friendly Cleaning Solutions
Water blasters, also known as pressure washers, use high-pressure water streams to clean surfaces without the need for abrasive materials. These blasters are ideal for tasks where environmental concerns are a priority, such as cleaning buildings, vehicles, or outdoor spaces. Their eco-friendly nature and versatility make them a popular choice for both industrial and residential applications.
What Makes Air Blasters Unique?
Air blasters are designed for material handling and flow optimization in industrial settings. These tools use compressed air to clear blockages in silos, hoppers, and pipelines. Their ability to maintain consistent material flow without causing damage makes them essential for industries like mining, agriculture, and manufacturing.
Dry Ice Blasters: Precision Cleaning Without Residue
Dry ice blasters use solid carbon dioxide pellets to clean surfaces without leaving behind any residue. This makes them ideal for sensitive environments, such as food processing plants or electronic manufacturing facilities. Dry ice blasters are also highly effective for removing grease, oil, and other stubborn contaminants.
Read also:Corey Haim And Charlie Sheen Friendship And Struggles Explored
Why Choose Shot Blasters for Surface Finishing?
Shot blasters are specialized tools used for surface finishing and preparation. They propel small steel shots at high speeds to create a smooth, uniform finish on metal surfaces. These blasters are commonly used in industries like aerospace and automotive manufacturing, where precision and quality are paramount.
Why Are Blasters Essential in Modern Industries?
Blasters have become a cornerstone of modern industries, thanks to their ability to streamline processes and deliver consistent results. Their versatility and efficiency make them indispensable across various sectors, from manufacturing to art restoration. Let’s delve into why blasters are so essential in today’s industrial landscape.
One of the primary reasons blasters are crucial is their ability to save time and labor. Tasks that would traditionally take hours or even days to complete manually can be accomplished in a fraction of the time using blasters. For example, removing rust from a large metal structure would require significant effort if done by hand, but a sandblaster can achieve the same result in a matter of minutes. This efficiency translates to cost savings and increased productivity, making blasters a smart investment for businesses.
Another key factor is the precision and control offered by blasters. Whether it’s etching intricate designs into glass or cleaning delicate machinery, blasters allow users to achieve exact results without compromising the integrity of the material. This level of precision is particularly important in industries like electronics and aerospace, where even the smallest error can have significant consequences. Additionally, blasters are highly customizable, allowing users to adjust settings such as pressure, nozzle size, and media type to suit specific tasks.
How to Choose the Right Blasters for Your Needs
Selecting the right blaster for your project can be a daunting task, given the wide variety of options available. However, by considering a few key factors, you can make an informed decision that ensures optimal performance and results. Below, we’ll outline the steps to help you choose the perfect blaster for your needs.
Assess the Task at Hand
The first step in choosing a blaster is to clearly define the task you need to accomplish. Are you looking to clean a surface, remove paint, or etch a design? Different tasks require different types of blasters and media. For instance, sandblasters are ideal for heavy-duty surface preparation, while dry ice blasters are better suited for delicate cleaning tasks.
Consider the Material and Surface
The material and surface you’re working on play a crucial role in determining the right blaster. For example, soft materials like wood or plastic may require lower pressure settings to avoid damage, while metal surfaces can withstand higher pressures. Additionally, consider the size of the area you need to cover, as this will influence the type of nozzle and hose you’ll need.
What Are the Key Features to Look For?
When evaluating blasters, pay attention to features such as portability, ease of use, and maintenance requirements. Portable blasters are ideal for on-site jobs, while larger, stationary models may be better suited for industrial settings. Look for models with adjustable settings, as these offer greater flexibility for different tasks. Additionally, consider the availability of replacement parts and customer support from the manufacturer.
Set a Budget and Compare Options
Blasters come in a wide range of prices, from affordable handheld models to high-end industrial machines. Set a budget based on your needs and compare options within that range. Keep in mind that while cheaper models may save you money upfront, they may lack the durability and performance of higher-end options. Reading reviews and seeking recommendations can also help you make an informed decision.
What Are the Safety Tips for Using Blasters?
While blasters are incredibly useful tools, they also come with inherent risks if not used properly. Understanding and adhering to safety guidelines is essential to prevent accidents and ensure a safe working environment. Below, we’ll explore some key safety tips to keep in mind when using blasters.
First and foremost, always wear appropriate personal protective equipment (PPE). This includes safety goggles, gloves, and a dust mask or respirator, depending on the type of blaster and media being used. PPE protects you from flying debris, dust, and other hazards that may arise during operation. Additionally, ensure that the work area is well-ventilated, especially when using abrasive materials or chemicals.
Another important safety tip is to inspect the equipment before use. Check for any signs of wear or damage, such as cracks in the hose or leaks in the compressor. Faulty equipment can lead to accidents, so it’s crucial to address any issues before starting a task. Furthermore, always follow the manufacturer’s instructions for operation and maintenance to avoid misuse.
Why Is Training Essential for Safe Blaster Use?
Proper training is vital for anyone using blasters, regardless of their experience level. Training ensures that users understand the equipment’s capabilities and limitations, as well as the potential risks involved. It also teaches users how to respond in case of emergencies, such as equipment malfunctions or accidental exposure to hazardous materials.
How Can You Minimize Environmental Impact?
In addition to personal safety, it’s important to consider the environmental impact of using blasters. For example, sandblasting can generate significant dust, which may pose health risks and environmental concerns. To minimize this, consider using eco-friendly alternatives like water blasters or dry ice blasters. Proper waste disposal and recycling of used media are also essential practices for reducing environmental harm.
Frequently Asked Questions About Blasters
What Are the Most Common Uses of Blasters?
Blasters are used in a wide range of applications, from industrial tasks like rust removal and surface preparation to creative projects like glass etching and art restoration. Their versatility makes them suitable for both heavy-duty and delicate tasks.
How Long Do Blasters Typically Last?
The lifespan of a blaster depends on factors such as the quality of the equipment, frequency of use, and maintenance practices. With proper care and regular maintenance, high-quality blasters can last for several years.
Are There Any Eco-Friendly Blasting Options?
Yes, eco-friendly options like water blasters and dry ice blasters are available. These tools minimize environmental impact by reducing waste and avoiding the use of harmful chemicals.
The Future of Blasters: Innovation and Advancements
The world of blasters is constantly evolving, with new technologies and innovations emerging to enhance their capabilities. From improved efficiency to eco-friendly designs, the future of blasters looks promising. Let’s explore some of the advancements that are shaping the industry.
One of the most exciting developments is the integration of smart technology into blasters. Modern blasters are now equipped with sensors and digital controls that allow users to monitor performance in real-time. These features not only improve precision but also enable predictive maintenance, reducing downtime and extending the lifespan of the equipment.
Another trend is the growing emphasis on sustainability. Manufacturers are increasingly focusing on developing
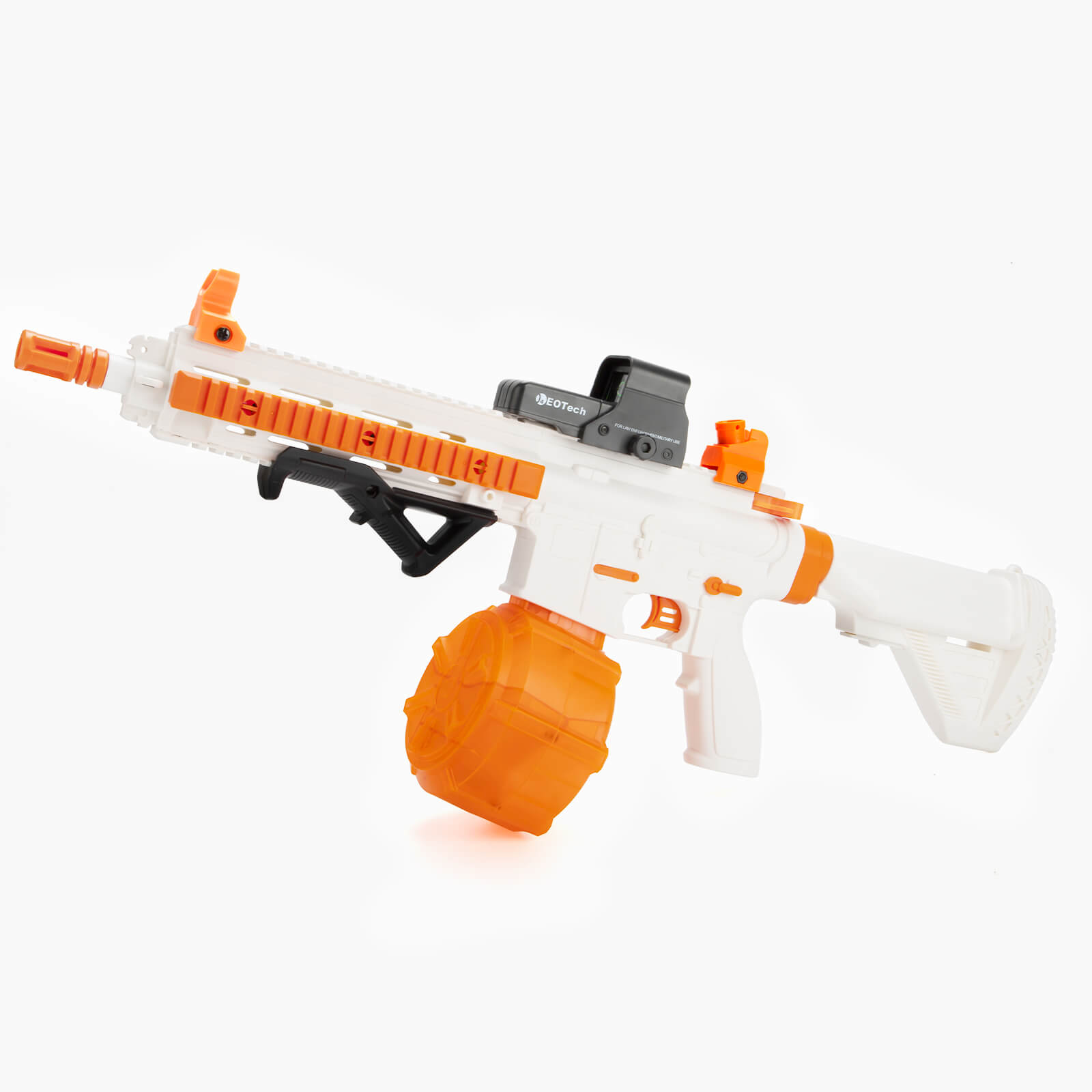
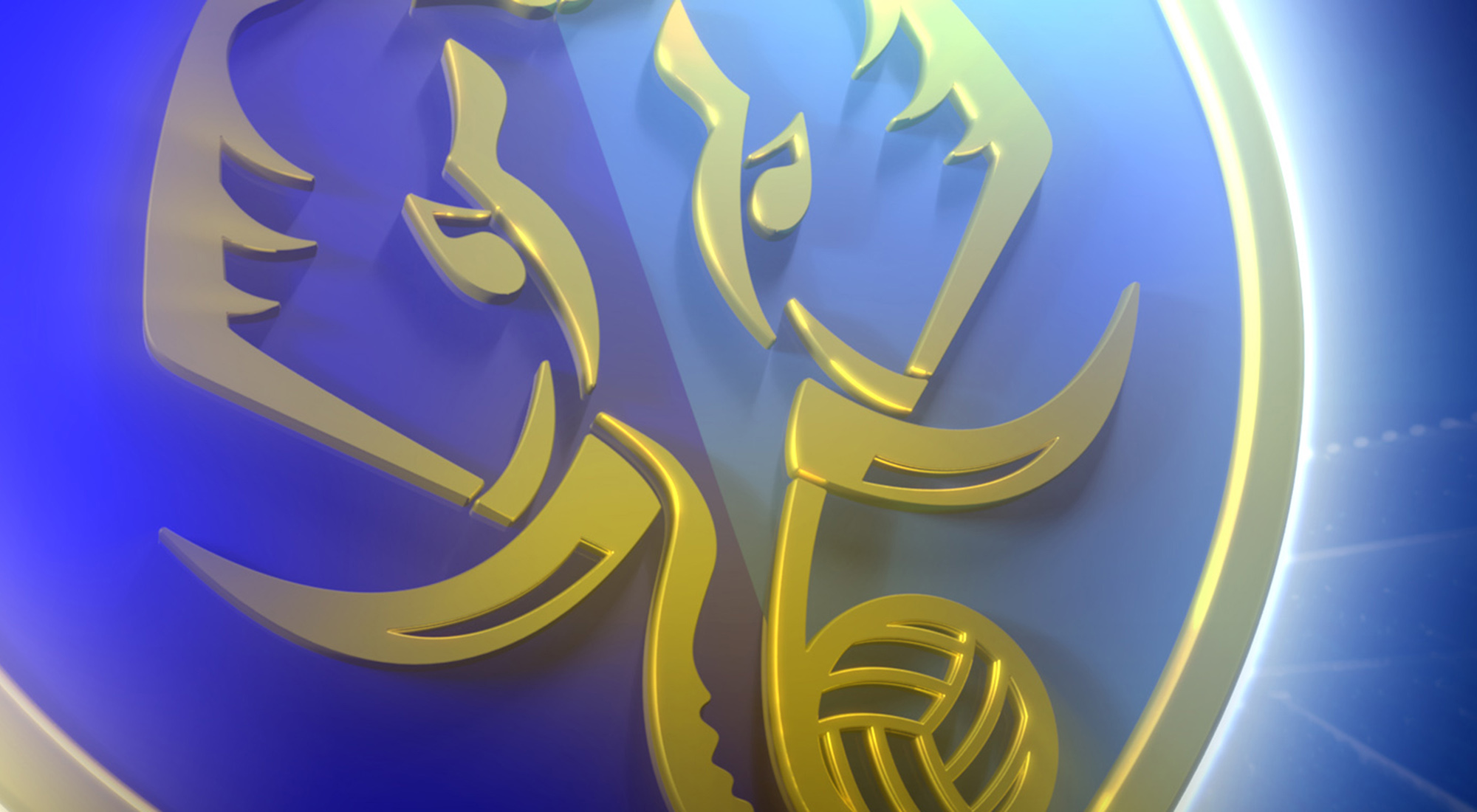