These accidents, often resulting from improper use of machinery, inadequate safety measures, or lack of training, have led to devastating consequences for workers and industries alike. The incidents highlight the critical need for stringent safety protocols and a deeper understanding of the risks associated with operating heavy machinery. With industrialization on the rise globally, understanding the factors contributing to such accidents is more important than ever. The Russian lathe accident is not just an isolated event but a reflection of broader issues within industrial environments. These accidents often occur in settings where safety regulations are either overlooked or poorly enforced. Workers operating lathes—a type of machine tool used to shape materials like metal or wood—are exposed to high-speed rotating components that pose significant risks if mishandled. The aftermath of such accidents can range from severe injuries to fatalities, leaving lasting impacts on families, communities, and industries. As such, it is crucial to examine the causes, consequences, and preventive measures to mitigate these risks effectively. This article delves into the multifaceted aspects of the Russian lathe accident, exploring its root causes, the role of safety protocols, and the lessons that can be learned to prevent future incidents. By understanding the human, technical, and systemic factors involved, we aim to provide a comprehensive analysis that not only informs but also empowers readers to advocate for safer industrial practices. Whether you're a worker, a safety professional, or simply someone interested in industrial safety, this article will equip you with the knowledge and tools to contribute to a safer workplace.
Table of Contents
- What Are the Primary Causes of Russian Lathe Accidents?
- How Can Workers Protect Themselves During Lathe Operations?
- What Role Does Training Play in Preventing Industrial Accidents?
- Examining the Consequences of the Russian Lathe Accident
- How Can Industries Implement Better Safety Protocols?
- Are There Global Lessons to Learn from Russian Lathe Incidents?
- The Future of Industrial Safety in Light of Lathe Accidents
- FAQs About Russian Lathe Accidents
What Are the Primary Causes of Russian Lathe Accidents?
Understanding the root causes of Russian lathe accidents is essential to preventing future incidents. These accidents often stem from a combination of human error, mechanical failure, and inadequate safety measures. Below, we explore the primary factors contributing to these unfortunate events:
Human Error: The Leading Culprit
One of the most significant contributors to lathe accidents is human error. This can include improper handling of the machine, failure to follow safety protocols, or even distractions while operating the equipment. For instance, workers may neglect to wear protective gear or fail to secure the material being worked on, leading to catastrophic outcomes. Did you know that studies show over 60% of industrial accidents are linked to human error? This statistic underscores the importance of vigilance and adherence to safety guidelines.
Read also:Maren Morris A Comprehensive Look At Her Life And Style
Machine Malfunctions and Maintenance Issues
Another critical factor is the condition of the lathe itself. Machines that are not regularly maintained or inspected can develop faults that increase the risk of accidents. Worn-out parts, faulty electrical systems, or misaligned components can all contribute to dangerous situations. Industries must prioritize routine maintenance and timely repairs to ensure the equipment remains in safe working condition.
Environmental Factors and Workplace Conditions
The environment in which the lathe is operated also plays a significant role. Poor lighting, cluttered workspaces, and inadequate ventilation can all contribute to accidents. Additionally, high-pressure work environments where productivity is prioritized over safety can lead to risky behaviors. Employers must create a culture that values safety as much as efficiency.
How Can Workers Protect Themselves During Lathe Operations?
While employers bear a significant responsibility for ensuring workplace safety, workers also play a crucial role in protecting themselves during lathe operations. Here are some practical steps workers can take to minimize risks:
Wearing Proper Personal Protective Equipment (PPE)
One of the simplest yet most effective ways to stay safe is by wearing appropriate PPE. This includes safety goggles to protect the eyes from flying debris, gloves to safeguard the hands, and sturdy footwear to prevent injuries from falling objects. Workers should ensure their PPE fits properly and is in good condition before starting any task.
Adhering to Safety Protocols
Every workplace should have established safety protocols for operating machinery like lathes. Workers must familiarize themselves with these guidelines and follow them meticulously. For example, ensuring the lathe is turned off before making adjustments or removing chips can prevent many accidents. Remember, cutting corners might save time, but it can cost lives.
Staying Alert and Focused
Operating heavy machinery requires full concentration. Workers should avoid distractions such as mobile phones or loud conversations while using the lathe. Additionally, taking regular breaks can help maintain focus and reduce fatigue, which is a common cause of accidents.
Read also:Decoding The Age Of Vicky Jain A Complete Overview
What Role Does Training Play in Preventing Industrial Accidents?
Training is a cornerstone of industrial safety, and its importance cannot be overstated when it comes to preventing accidents like the Russian lathe incident. Proper training equips workers with the knowledge and skills needed to operate machinery safely and respond effectively in emergencies.
The Importance of Hands-On Training
Theoretical knowledge is essential, but hands-on training is equally critical. Workers should have the opportunity to practice operating lathes under the supervision of experienced trainers. This allows them to gain confidence and learn how to handle unexpected situations without risking their safety.
Continuous Learning and Refresher Courses
Safety protocols and technologies evolve over time, making continuous learning necessary. Employers should provide regular refresher courses to ensure workers stay updated on the latest safety practices. This not only reinforces existing knowledge but also introduces new techniques that can further reduce risks.
Examining the Consequences of the Russian Lathe Accident
The consequences of the Russian lathe accident extend far beyond the immediate injuries or fatalities. These incidents have profound impacts on individuals, families, and industries, often leading to long-term physical, emotional, and financial burdens.
Physical and Emotional Toll on Workers
Victims of lathe accidents often suffer severe injuries such as amputations, fractures, or burns. These injuries can result in permanent disabilities, affecting the individual's ability to work and lead a normal life. Moreover, the psychological impact, including trauma and anxiety, can linger for years, requiring ongoing support and counseling.
Financial Implications for Families and Companies
Accidents also impose significant financial burdens. Medical expenses, rehabilitation costs, and loss of income can devastate families. For companies, the costs include compensation claims, legal fees, and potential fines for violating safety regulations. These financial repercussions highlight the importance of investing in safety measures to prevent accidents.
Impact on Industrial Reputation
Companies involved in such accidents often face reputational damage, leading to loss of trust among clients, partners, and the public. This can result in reduced business opportunities and a decline in market share. Prioritizing safety not only protects workers but also safeguards the company's reputation.
How Can Industries Implement Better Safety Protocols?
To prevent accidents like the Russian lathe incident, industries must adopt a proactive approach to safety. This involves implementing robust protocols, fostering a safety-first culture, and leveraging technology to enhance workplace safety.
Developing Comprehensive Safety Policies
Industries should create detailed safety policies that address every aspect of lathe operation, from machine maintenance to emergency response. These policies should be easily accessible to all employees and regularly reviewed to ensure they remain relevant and effective.
Encouraging a Safety-First Culture
A safety-first culture starts at the top. Company leaders must prioritize safety and communicate its importance to all employees. This can be achieved through regular safety meetings, recognition programs for safe practices, and open channels for reporting hazards or concerns.
Leveraging Technology for Enhanced Safety
Advancements in technology offer new opportunities to improve safety. For example, sensors can monitor machine performance and alert operators to potential issues. Virtual reality (VR) training programs can simulate hazardous scenarios, allowing workers to practice responding to emergencies without risk.
Are There Global Lessons to Learn from Russian Lathe Incidents?
The Russian lathe accident serves as a wake-up call for industries worldwide. While the incident may have occurred in a specific region, the lessons it offers are universally applicable. By analyzing these incidents, industries can identify common pitfalls and implement measures to prevent similar accidents.
Standardizing Safety Practices Across Borders
One key takeaway is the need for standardized safety practices across industries and countries. While regulations may vary, the principles of safety remain constant. Collaborative efforts to establish global safety standards can help ensure consistency and reduce the risk of accidents.
Sharing Knowledge and Best Practices
Sharing knowledge and best practices is another critical lesson. Industries should actively participate in forums, conferences, and workshops to exchange insights and learn from each other's experiences. This collective approach fosters innovation and continuous improvement in safety practices.
Investing in Research and Development
Finally, investing in research and development can lead to breakthroughs in safety technology. By exploring new materials, designs, and systems, industries can create safer working environments and reduce the likelihood of accidents.
The Future of Industrial Safety in Light of Lathe Accidents
As industries continue to evolve, so too must their approach to safety. The Russian lathe accident highlights the need for a forward-thinking mindset that embraces innovation, education, and collaboration to create safer workplaces.
Embracing Automation and Robotics
Automation and robotics offer promising solutions to reduce human exposure to hazardous tasks. By integrating these technologies into industrial processes, companies can minimize risks and enhance productivity simultaneously.
Promoting Lifelong Learning
Safety education should not end with initial training. Promoting lifelong learning ensures that workers remain informed about the latest safety practices and technologies. Online courses, workshops, and certifications can help workers stay ahead of the curve.
Collaborating for a Safer Future
Finally, collaboration between governments, industries, and educational institutions is essential to advancing industrial safety. By working together, these stakeholders can develop policies, programs, and innovations that prioritize worker safety and well-being.
FAQs About Russian Lathe Accidents
What Should I Do If I Witness a Lathe Accident?
If you witness a lathe accident, the first step is to ensure your own safety. Then, immediately alert the authorities and provide first aid if you are trained to do so. Reporting the incident promptly can help prevent further injuries and ensure proper documentation.
How Can Companies Be Held Accountable for Lathe Accidents?
Companies can be held accountable through legal action, regulatory fines, and public scrutiny. Ensuring compliance with safety regulations and maintaining transparent communication with stakeholders can help companies avoid liability and demonstrate their commitment to safety.
Are There Any New Technologies to Prevent Lathe Accidents?
Yes, advancements such as machine sensors, AI-driven monitoring systems, and VR training programs are being developed to enhance safety. These technologies can detect potential hazards, provide real-time alerts, and simulate emergency scenarios for training purposes.
Conclusion
The Russian lathe accident is a stark reminder of the importance of industrial safety. By understanding its causes, consequences, and preventive measures, we can work towards creating safer workplaces for everyone. Through education, innovation, and collaboration, industries can reduce the risk of accidents and ensure a brighter, safer future.
For more information on industrial safety, visit the
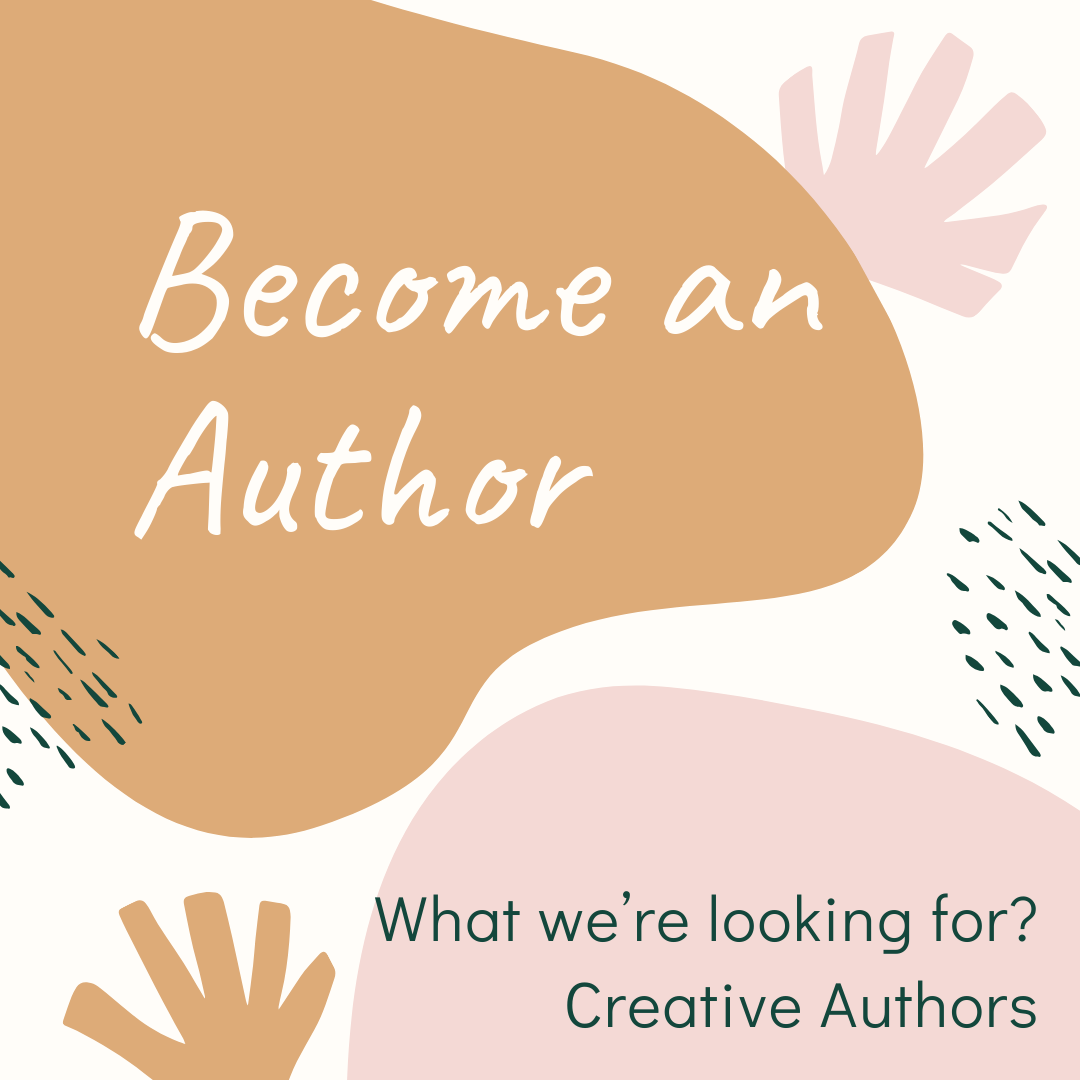
