In recent years, a series of industrial accidents involving lathes have gained significant attention, particularly those documented in videos like the infamous "Russian lathe accident video." These videos serve as grim reminders of the potential dangers associated with operating heavy machinery in industrial environments. The footage often showcases the catastrophic consequences of neglecting safety protocols, making it a topic of both curiosity and concern. While these videos may be unsettling, they play a critical role in raising awareness about the importance of adhering to safety guidelines. By examining these incidents, we can better understand the risks involved and take proactive steps to prevent similar tragedies in the future.
Industrial accidents, especially those involving lathes, are not uncommon. These machines, while essential for manufacturing and metalworking, require precision, focus, and strict adherence to safety measures. The "Russian lathe accident video" has become a pivotal example of what can go wrong when these protocols are ignored. The video has sparked discussions across forums, social media, and professional circles, prompting calls for improved safety training and stricter enforcement of workplace regulations. It also highlights the need for workers to remain vigilant and for employers to prioritize safety over productivity.
Despite the unsettling nature of these videos, they provide a valuable opportunity to learn from past mistakes. By analyzing the circumstances surrounding the "Russian lathe accident video," we can identify common risk factors and develop strategies to mitigate them. This article delves into the details of such incidents, explores the reasons behind their occurrence, and offers practical advice on how to ensure safety in industrial settings. Whether you're a seasoned professional or someone new to the field, this comprehensive guide will equip you with the knowledge needed to stay safe while operating lathes and other heavy machinery.
Read also:Jake Andersons Fitness Journey A Deep Dive Into His Weight Transformation
Table of Contents
- What Happened in the Russian Lathe Accident Video?
- Why Do Lathe Accidents Happen? Common Causes and Risk Factors
- How Can Workers Prevent Lathe Accidents?
- What Are the Safety Protocols for Operating Lathes?
- Why Is Proper Training Essential for Lathe Operators?
- How Can Employers Ensure a Safe Work Environment?
- What Lessons Can Be Learned from the Russian Lathe Accident Video?
- FAQs About Lathe Safety and Accidents
What Happened in the Russian Lathe Accident Video?
The "Russian lathe accident video" has become a widely discussed incident in industrial safety circles. While the exact details of the video may vary depending on the source, the general narrative involves a worker operating a lathe without adhering to proper safety measures. The video captures a moment when the operator, likely distracted or improperly trained, comes into contact with the rotating components of the machine. This results in severe injuries, underscoring the critical importance of following safety protocols.
One of the most striking aspects of the video is how quickly the situation escalates. The operator appears to be wearing loose clothing, which gets caught in the lathe's rotating spindle. Within seconds, the force of the machine pulls the operator closer, leading to a catastrophic outcome. This incident highlights the dangers of neglecting even the most basic safety precautions, such as wearing fitted clothing and using protective equipment. It also raises questions about the level of supervision and training provided to workers in such environments.
While the video serves as a cautionary tale, it has also sparked debates about the ethics of sharing such footage. Some argue that it provides a valuable learning opportunity, while others believe it sensationalizes industrial accidents. Regardless of one's stance, the "Russian lathe accident video" has undoubtedly drawn attention to the need for improved safety measures in industrial settings. By examining the sequence of events and the factors that contributed to the accident, we can identify key areas for improvement and prevent similar incidents in the future.
Why Do Lathe Accidents Happen? Common Causes and Risk Factors
Lathe accidents, like the one depicted in the "Russian lathe accident video," are often the result of a combination of factors. Understanding these causes is essential for preventing future incidents. One of the most common risk factors is operator error. This can include failing to follow safety protocols, using the machine incorrectly, or attempting to adjust the lathe while it is still in operation. Distractions, fatigue, and inadequate training can all contribute to these mistakes.
Another significant cause of lathe accidents is the lack of proper safety equipment. Many operators neglect to wear protective gear such as gloves, goggles, or fitted clothing. Loose clothing, in particular, poses a major hazard, as it can easily get caught in the machine's moving parts. Additionally, some workplaces fail to provide adequate safeguards, such as machine guards or emergency stop buttons, further increasing the risk of accidents.
Environmental factors also play a role in lathe accidents. Poor lighting, cluttered workspaces, and insufficient maintenance of equipment can create hazardous conditions. Employers must ensure that their facilities are well-organized and that machinery is regularly inspected and serviced. By addressing these common causes and risk factors, we can significantly reduce the likelihood of lathe accidents and create safer work environments for everyone.
Read also:Yuli Gurriels Contract Insight Into The Baseball Stars Deal
How Can Workers Prevent Lathe Accidents?
Preventing lathe accidents requires a proactive approach from both workers and employers. For workers, the first step is to undergo comprehensive training that covers not only the technical aspects of operating a lathe but also the safety protocols that must be followed. This includes understanding the machine's components, recognizing potential hazards, and knowing how to respond in emergency situations. Regular refresher courses can help reinforce this knowledge and keep safety top of mind.
In addition to training, workers should always wear appropriate personal protective equipment (PPE). This includes safety goggles to protect the eyes from flying debris, fitted clothing to prevent entanglement, and gloves to safeguard the hands. It's also crucial to remove any jewelry or accessories that could get caught in the machine. Workers should never attempt to adjust or clean the lathe while it is in operation and should always use tools specifically designed for the task.
Another key strategy is to stay focused and avoid distractions while operating a lathe. This means keeping the workspace clean and organized, ensuring adequate lighting, and taking regular breaks to prevent fatigue. By adopting these practices, workers can minimize the risk of accidents and contribute to a safer work environment. Employers, too, have a responsibility to support their employees by providing the necessary resources and fostering a culture of safety.
What Are the Safety Protocols for Operating Lathes?
Operating a lathe safely requires strict adherence to established safety protocols. These guidelines are designed to protect workers from the inherent risks associated with these powerful machines. One of the most fundamental rules is to always wear personal protective equipment (PPE). This includes safety goggles to shield the eyes from metal shavings and other debris, fitted clothing to prevent entanglement, and sturdy footwear to protect the feet from falling objects.
Before starting the machine, operators should conduct a thorough inspection to ensure that all components are in good working condition. This includes checking the spindle, chuck, and tool holders for signs of wear or damage. Any issues should be reported and addressed immediately. Additionally, machine guards should be in place to prevent accidental contact with moving parts. Operators should also familiarize themselves with the location of the emergency stop button and know how to use it in case of an emergency.
During operation, it's crucial to maintain a safe distance from the lathe's rotating components and avoid reaching into the machine while it is in motion. Tools should be used only for their intended purpose, and adjustments should only be made after the machine has been turned off and come to a complete stop. By following these safety protocols, operators can significantly reduce the risk of accidents and ensure a safer working environment for everyone.
Why Is Proper Training Essential for Lathe Operators?
Proper training is the cornerstone of safe and efficient lathe operation. Without adequate instruction, operators are more likely to make mistakes that can lead to serious accidents. Training programs should cover both the technical aspects of using a lathe and the safety measures that must be followed. This includes understanding the machine's components, learning how to set up and operate the equipment, and recognizing potential hazards.
One of the key benefits of proper training is that it instills a sense of confidence in operators. When workers feel competent and knowledgeable, they are less likely to make errors caused by uncertainty or hesitation. Training also helps operators develop good habits, such as wearing PPE, keeping the workspace clean, and conducting pre-operation checks. These habits can significantly reduce the risk of accidents and contribute to a safer work environment.
Employers should invest in ongoing training programs to ensure that their workers stay up to date with the latest safety standards and best practices. This includes offering refresher courses and providing opportunities for workers to ask questions and share their experiences. By prioritizing training, employers can demonstrate their commitment to safety and empower their employees to operate lathes with confidence and competence.
How Can Employers Ensure a Safe Work Environment?
Employers play a critical role in ensuring a safe work environment for lathe operators and other industrial workers. One of the most important steps is to provide comprehensive safety training that covers all aspects of machine operation and hazard prevention. This training should be mandatory for all employees and include both theoretical instruction and hands-on practice. Employers should also ensure that their workers have access to the necessary personal protective equipment (PPE) and that they understand how to use it correctly.
Another key responsibility for employers is to maintain their equipment and facilities in good working condition. This includes conducting regular inspections of lathes and other machinery to identify and address any issues before they become hazards. Employers should also ensure that their workspaces are well-organized, with adequate lighting and clear pathways to prevent trips and falls. Providing machine guards and emergency stop buttons is another essential measure to enhance safety.
Finally, employers should foster a culture of safety by encouraging open communication and accountability. Workers should feel comfortable reporting hazards or unsafe practices without fear of reprisal. By prioritizing safety and leading by example, employers can create a work environment where everyone feels valued and protected. This not only reduces the risk of accidents but also boosts morale and productivity.
What Lessons Can Be Learned from the Russian Lathe Accident Video?
The "Russian lathe accident video" serves as a powerful reminder of the importance of safety in industrial settings. One of the most significant lessons is the critical role of proper training and adherence to safety protocols. The video highlights how quickly things can go wrong when operators neglect basic precautions, such as wearing fitted clothing or using protective equipment. It underscores the need for employers to provide comprehensive training and ensure that their workers are fully prepared to operate machinery safely.
Another key takeaway is the importance of maintaining a safe work environment. The video reveals how environmental factors, such as cluttered workspaces and inadequate machine guards, can contribute to accidents. Employers must prioritize regular maintenance of equipment and ensure that their facilities are well-organized and free of hazards. By addressing these issues proactively, they can significantly reduce the risk of accidents and create a safer workplace for everyone.
Finally, the video highlights the ethical responsibility of sharing such footage. While it provides a valuable learning opportunity, it also raises questions about the potential for sensationalism. By focusing on the lessons learned rather than the shock value, we can use incidents like the "Russian lathe accident video" to drive meaningful change and improve safety standards in industrial settings.
FAQs About Lathe Safety and Accidents
What should I do if I witness a lathe accident?
If you witness a lathe accident, the first step is to ensure your own safety and avoid putting yourself in harm's way. Immediately activate the emergency stop button on the machine, if possible, to prevent further injury. Next, notify a supervisor or call emergency services to ensure that the injured person receives prompt medical attention. Avoid moving the injured individual unless absolutely necessary, as this could worsen their condition. After the situation is under control, document the incident and report it to the appropriate authorities for investigation.
How often should lathe operators receive safety training?
Lathe operators should receive safety training at least once a year, with additional sessions provided whenever new equipment or procedures are introduced. Regular refresher courses are
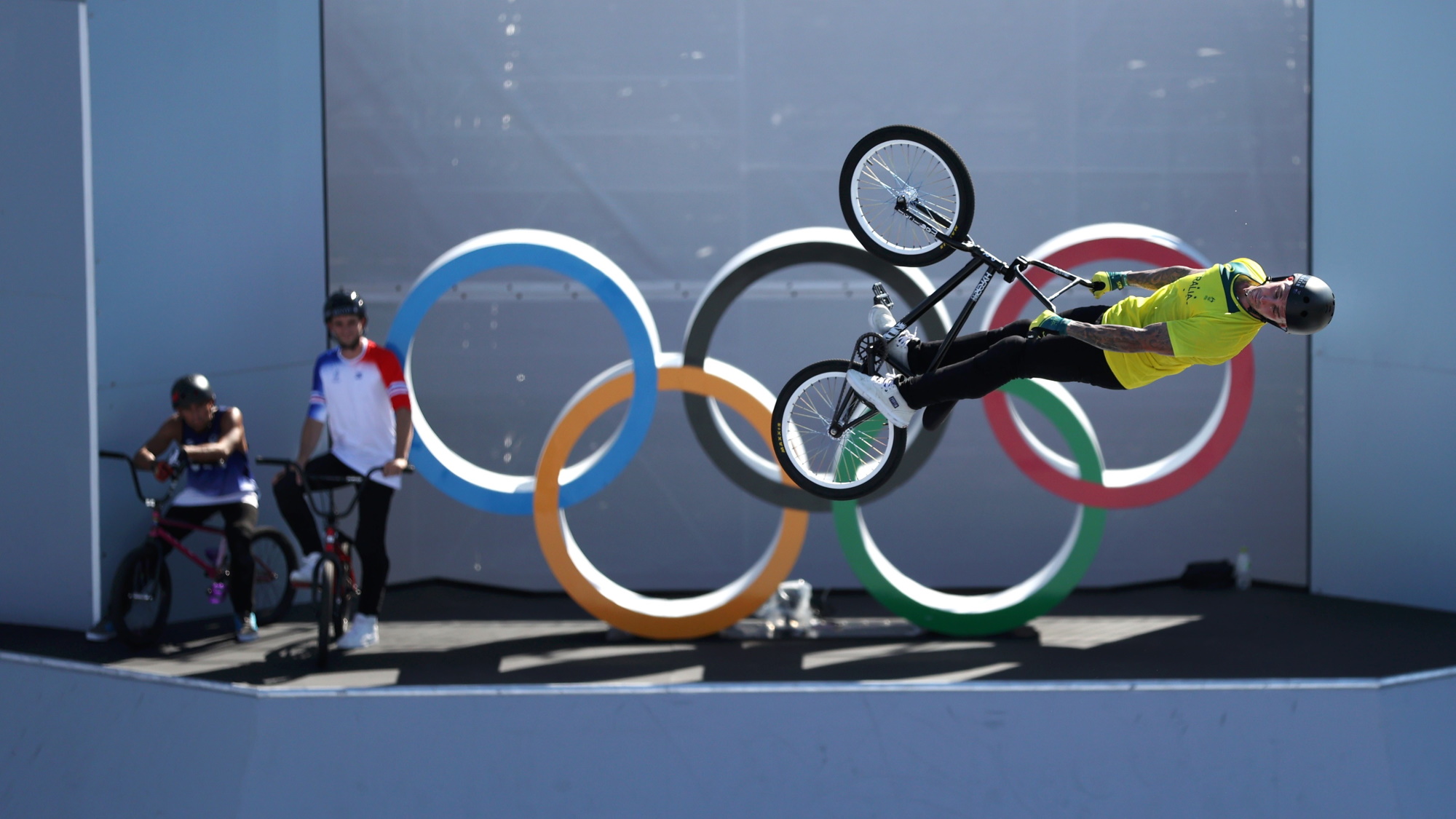